1.What is a waterproof stepper motor?
The waterproof stepper motor is an electric device with waterproof function, which is suitable for various scenarios that require waterproof protection. It has the advantages of high reliability, wide adaptability and easy use. The waterproof stepper motor adopts special materials and sealing design to effectively prevent moisture from invading the interior, thereby improving the reliability of the equipment. Even in a humid or rainy environment, the stepper motor can work normally and is not easily corroded or damaged by moisture. In addition, waterproof stepper motors are suitable for multiple fields, such as industrial automation, smart home, medical equipment, etc. In industrial automation, it can be used for the control of robotic arms, process equipment, etc.; in smart home, it can be applied to the drive of smart curtains, smart door locks, etc.; in medical equipment, it can be used for precise control of surgical robots, etc. Whether indoors or outdoors, waterproof stepper motors can operate stably. The installation is simple, just follow the instructions to connect, usually with a standard foot bottom hole layout, suitable for various fixing methods. At the same time, the control of waterproof stepper motors is also very flexible. It can be operated by switches, remote controls, mobile phones and other methods. No matter where you are, you can easily control the device.
1.Stator: Contains the iron core and coils. The iron core is stationary, while the coils are tightly wound around the iron core. When current passes through the coil, a magnetic field is generated, which interacts with the magnetic field of the rotating part to drive the rotation of the rotating part.
2.Rotor: Forms an integral unit with the shaft and is firmly connected to the housing through bearings. Under the action of the magnetic field, the rotor interacts with the magnetic field of the stator coil to enable it to rotate.
3.Shaft: It is the connecting part between the rotor and the housing, allowing the rotor to rotate freely inside the housing.
4.Housing: Protects the internal components of the stepper motor and provides a mounting base so that the stepper motor can be easily installed in the desired location.
5.Sealing design: Including the use of rubber sealing rings, sealants, etc., to form an effective seal at the key interfaces of the motor to prevent the entry of water and particulate matter. The special housing design can also prevent water and particles from entering the motor through the housing.
6.Drive circuit: It is mainly composed of components such as drive chips, power transistors, capacitors and resistors. This circuit is responsible for regulating the direction and intensity of the current, thereby controlling the start, stop, direction and speed of the stepper motor.
7.Sensors: They play an important role in stepper motors. They can monitor the position and speed of the motor in real time and feed this information back to the control system to ensure precise control of the motor.
3.Waterproof requirements for waterproof stepper motors
1.Use waterproof sealing structure: Use a waterproof sealing structure between the motor housing and the end cover to prevent moisture from entering the motor.
2.Use waterproof bearings: Use bearings with waterproof function to prevent moisture from entering the motor from the bearings.
3.Use waterproof cables: Use cables and connectors with waterproof function to prevent moisture from entering the motor from the cables.
4.Use waterproof coating: Spray waterproof coating on the surface of the motor to prevent moisture from entering the motor from the surface.
5.Sealing design: Use sealing materials such as sealing gaskets, sealants or O-rings at key components and connections to ensure that the inside of the motor is isolated from the external environment.
6.Use coatings and materials with excellent water corrosion resistance and waterproof performance: Such as stainless steel, nickel alloy, ceramic coating, etc. to prevent water penetration and corrosion.
7.Use waterproof joints and connectors: Ensure that the connection points between the cable and the motor are not intruded by water.
8.Use waterproof cables: Ensure that the cables can work reliably for a long time in underwater environments.
9.Use junction boxes and waterproof covers: Protect the wiring and connection points inside the motor to prevent water infiltration.
10.Test and verify: Perform strict testing and verification before manufacturing to ensure that the waterproof performance meets the requirements, including pressure testing, water tightness testing, and performance testing.
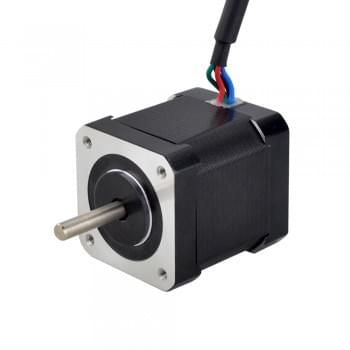
1.Wiring: According to the model and use requirements of the stepper motor, correctly connect the control signal line, power line, enable signal line, direction signal line, etc. Ensure that all cables are securely connected. Especially when used in industrial sites, shielding issues should be considered to avoid connecting all required cables at the beginning. Instead, connect the most basic system first, and then gradually connect other cables after it runs well.
2.Controller settings: Set the drive current, pulse number and other parameters of the stepper motor through the controller. The controller can be a single-chip microcomputer, motion control card and other devices. Make sure that the motor model or current setting value matches the setting on the drive controller.
3.Operation observation: Within half an hour after the motor starts running, closely observe the status of the motor, such as whether the movement is normal, the sound and temperature rise. If any problems are found, stop and adjust immediately.
4.Waterproof measures: Use special housings and waterproof shaft seals to protect the motor, especially the shaft and bearing parts. Special housings and waterproof shaft seals create a closed area for the internal workings of the motor to prevent water damage.
5.Protection level: Select the appropriate protection level according to the use environment. For example, the IP68 level means complete protection against foreign objects and dust intrusion, and prevents water intrusion when sinking. Motors used in harsh conditions, such as new energy vehicle drive motors or motors on fishing boats, generally require a higher level of protection.